Readily available R&D material on Chamfr.com
Westlake Plastics makes it easy for engineers and product developers to work with our materials by offering a variety of products in small quantities for developmental projects and prototyping on Chamfr. If you’re in quick need of semi-finished stock shape materials for your next R&D project, go on over to Chamfr.com. Westlake materials currently available on Chamfr include;
Lennite (UHMW-PE) 12” rods (1”, 2”, 3.25” Diameters)
Radel (PPSU) 12” rods (1”, 2”, 3” Diameters)
Propylux HS (PP) 12” rods (1”, 2”, 3” Diameters)
Propylux HS2 (PP) 12” x 12” sheets (0.5”, 1.5”, 2.0” Thicknesses)
Readily available R&D material on Chamfr.com
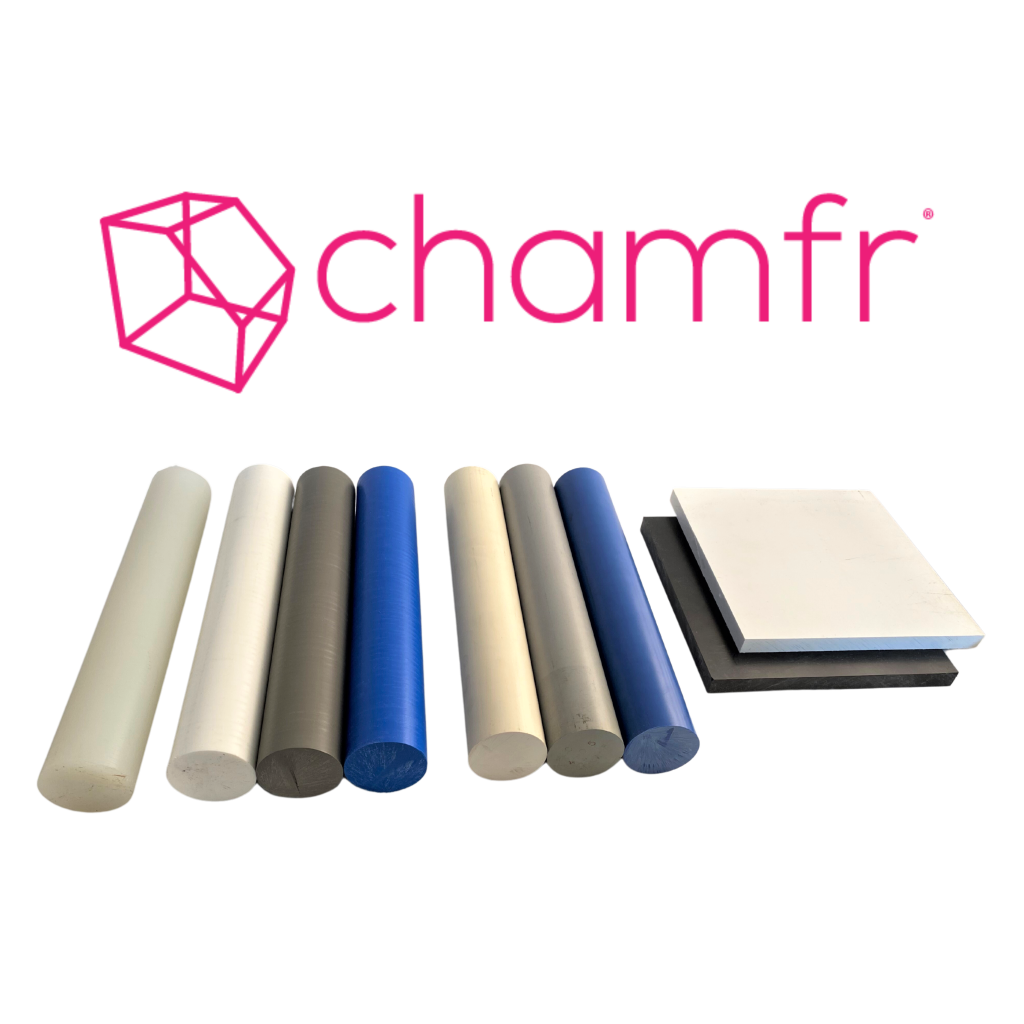
Westlake Plastics makes it easy for engineers and product developers to work with our materials by offering a variety of products in small quantities for developmental projects and prototyping on Chamfr. If you’re in quick need of semi-finished stock shape materials for your next R&D project, go on over to Chamfr.com. Westlake materials currently available on Chamfr include;
Lennite (UHMW-PE) 12” rods (1”, 2”, 3.25” Diameters)
Radel (PPSU) 12” rods (1”, 2”, 3” Diameters)
Propylux HS (PP) 12” rods (1”, 2”, 3” Diameters)
Propylux HS2 (PP) 12” x 12” sheets (0.5”, 1.5”, 2.0” Thicknesses)
NEW COLORS FOR PRODUCT DEVELOPMENT
Whether it be for branding purposes, to create aesthetic value to differentiate your product or for functional color coding purposes, color can be a significant part of your product offering. Westlake offers several of our products in a range of standard colors. If standard colors do not meet your requirements, we can work with you to develop new colors. By utilizing our partnerships with custom compounders, Westlake Plastics can modify the color of most materials.
NEW COLORS FOR PRODUCT DEVELOPMENT
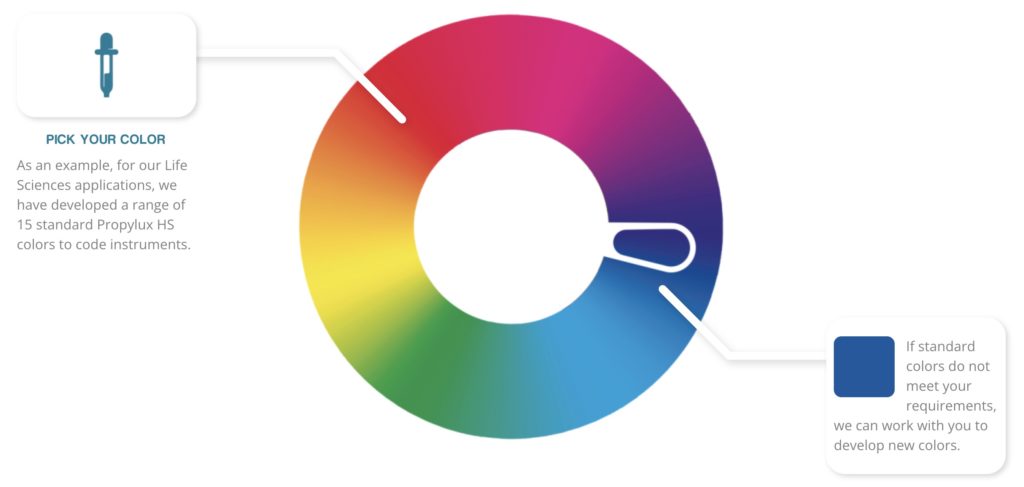
Whether it be for branding purposes, to create aesthetic value to differentiate your product or for functional color coding purposes, color can be a significant part of your product offering. Westlake offers several of our products in a range of standard colors. If standard colors do not meet your requirements, we can work with you to develop new colors. By utilizing our partnerships with custom compounders, Westlake Plastics can modify the color of most materials.
CUSTOM SIZES FOR NEW PRODUCT DEVELOPMENT
Westlake has extrusion tooling to produce most standard rod diameters. If custom sizes are required, we can work with you to develop new tooling to improve your yields. For sheet and film, we can customize the thickness to improve your yields and reduce your manufacturing costs, saving you time and money.
CUSTOM SIZES FOR NEW PRODUCT DEVELOPMENT
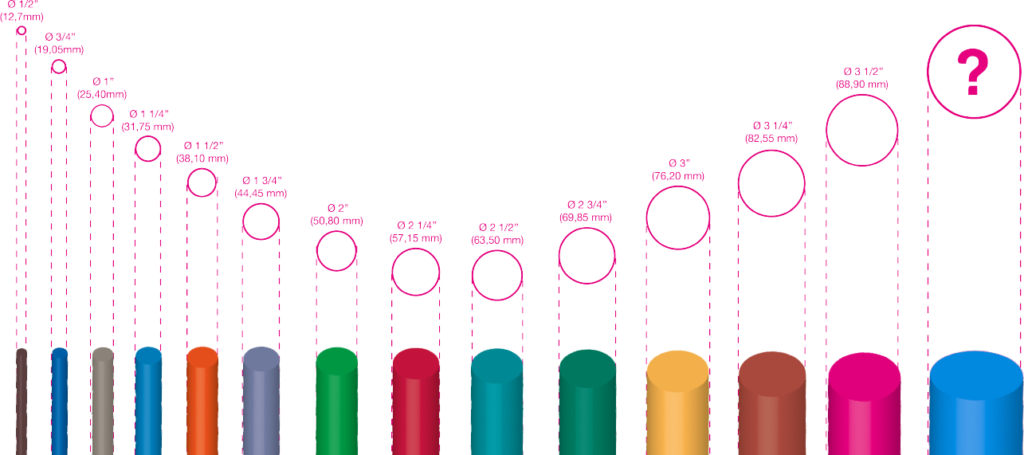
Westlake has extrusion tooling to produce most standard rod diameters. If custom sizes are required, we can work with you to develop new tooling to improve your yields. For sheet and film, we can customize the thickness to improve your yields and reduce your manufacturing costs, saving you time and money.
CASE STUDY
Our engagement with Intech Medical focused around helping them select a polymer that would retain its toughness and ductility. We collaborated with them to develop and execute a testing protocol to show how part performance would vary over time after repeated cleaning and steam sterilization cycles. While alternative polymers were evaluated, PROPYLUX® HS showed the best performance
CASE STUDY
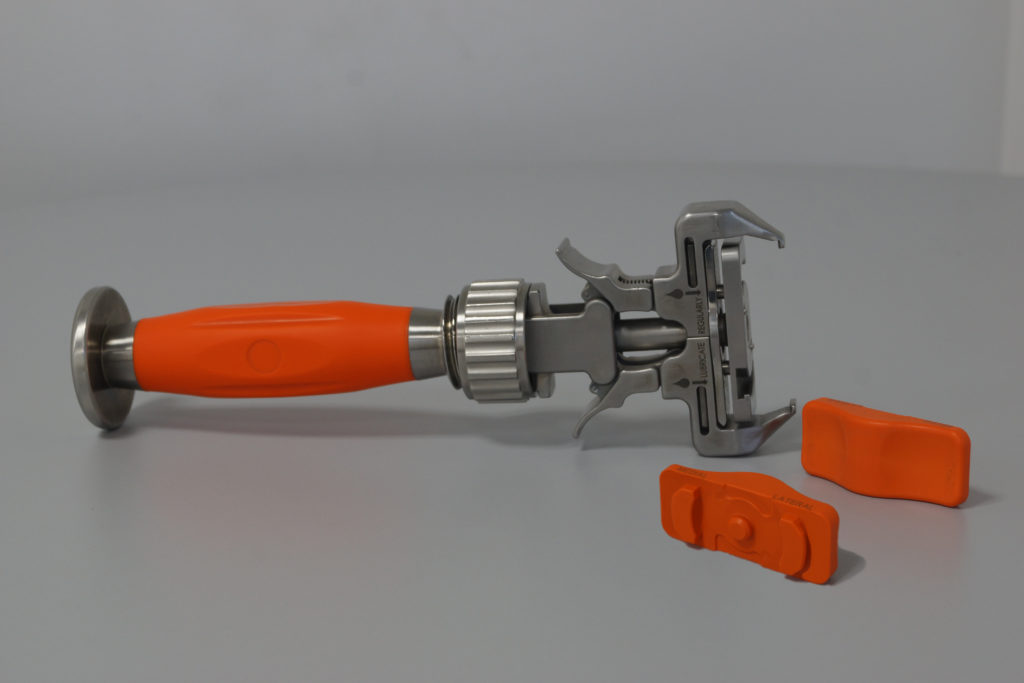
Our engagement with Intech Medical focused around helping them select a polymer that would retain its toughness and ductility. We collaborated with them to develop and execute a testing protocol to show how part performance would vary over time after repeated cleaning and steam sterilization cycles. While alternative polymers were evaluated, PROPYLUX® HS showed the best performance
NEW SHAPES
For higher value materials, Westlake is innovating by developing shapes that reduce scrap rates as well as machine time. Using our compression molding technologies, we are building molds to provide near-net shapes, resulting in lower material costs.
NEW SHAPES
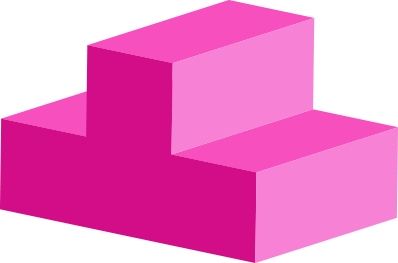
For higher value materials, Westlake is innovating by developing shapes that reduce scrap rates as well as machine time. Using our compression molding technologies, we are building molds to provide near-net shapes, resulting in lower material costs.
Property Modification
If you need a material to meet critical performance requirements or industry specific standards that an off the shelf product can’t address we can help by developing a custom modified product. Utilizing our partnerships with custom compounders, and our expertise in extrusion and compression molding Westlake Plastics can help you solve your next material challenge. Performance attributes we can help address include:
Property Modification
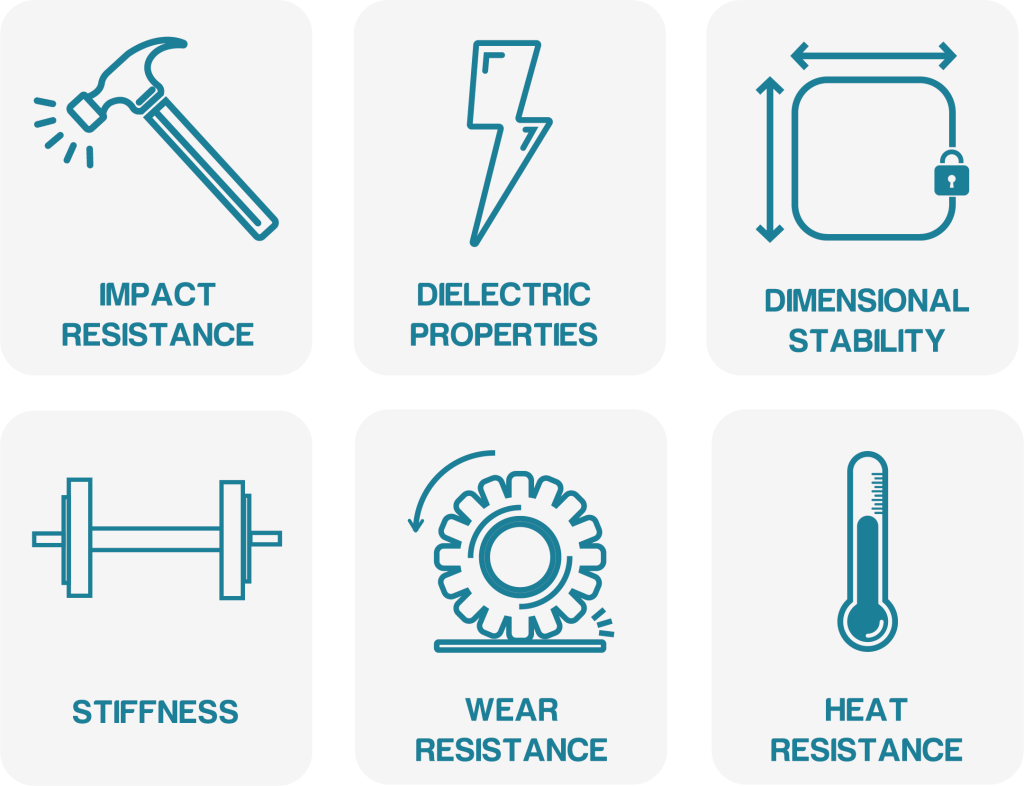
If you need a material to meet critical performance requirements or industry specific standards that an off the shelf product can’t address we can help by developing a custom modified product. Utilizing our partnerships with custom compounders, and our expertise in extrusion and compression molding Westlake Plastics can help you solve your next material challenge. Performance attributes we can help address include:
NEW POLYMERS
Westlake Plastics partners with the leading polymer manufacturers to process new polymers into useable forms.
NEW POLYMERS
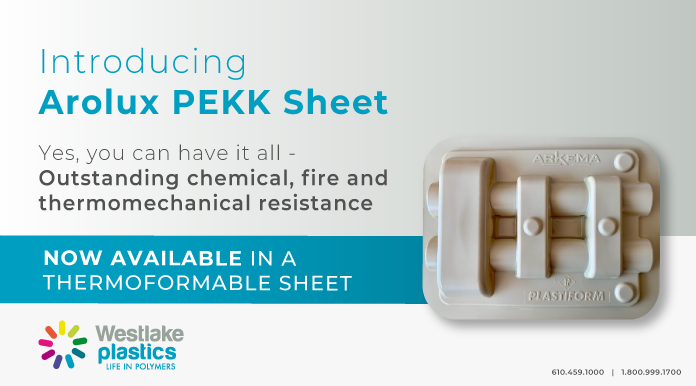
Westlake Plastics partners with the leading polymer manufacturers to process new polymers into useable forms.
Additional Product Development Content
To learn more about individual products you can head over to our products page or check out extra product information.