Attributes
Biocompatibility

Westlake Plastics understands the compositional attributes and performance characteristics that thermoplastics must meet to be considered biocompatible for medical and life science applications. We also adhere to the domestic and global standards which define and govern biocompatibility compliance of thermoplastics.
Materials that are considered biocompatible do not produce a toxic or immunological response when exposed to the body or bodily fluids. There are two testing standards for biocompatible products, ISO 10993 and protocols defined by USP. ISO 10993 determines whether a material is biocompatible for use in medical devices, whereas USP protocols determine whether a material is biocompatible for use in pharmaceutical applications. Following either standard, the aim is to certify that there are no harmful reactions or long-term bodily effects caused by the materials in direct contact with the patient or through contact with pharmaceutical products that would be injected or ingested by a patient. Analysis includes leachables and extractables testing. In vivo and in vitro evaluations are often used to test for cytotoxicity, hemocompatibility, genotoxicity, irritation, implantation, sensitization, and systemic toxicity. Biocompatible plastics must also not degrade after sterilization.
Our entire approach—from product design through manufacturing and quality control—is designed to ensure that our products meet the precise performance and biocompatibility compliance and traceability requirements for the application. For example, we ram-extrude our biocompatible Lennite, an ultra-high molecular weight polyethylene material, for orthopedic implant applications.
Biocompatibility
Impact Resistance
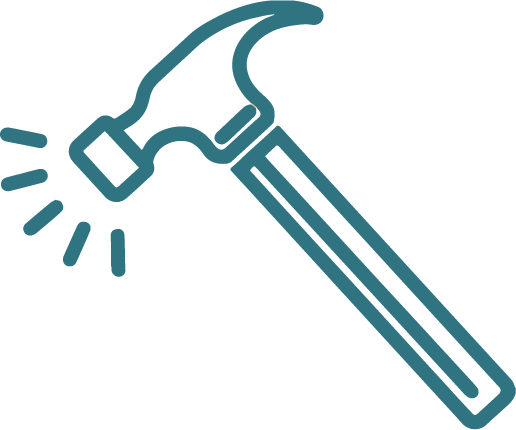
Impact resistance is a material’s ability to withstand intense force or shock applied to it over a short period of time. This is an important physical characteristic for materials that are used in harsh environments or could be damaged if dropped. Impact resistance is a measure of a material’s ductility and strength. Ductility is the ability of a material to deform or be strained without fracture, and strength is a measure of a material’s ability to carry or transmit a load. Thus, impact resistance is the ability of a material to absorb energy and plastically deform without fracturing. Factors that affect the impact resistance of a plastic include its molecular weight, molecular structure, and morphology (amorphous vs crystalline). The two common methods for testing impact resistance are the Izod Impact Test and the Charpy Impact Test.
Zelux is Westlake Plastics’ family of polycarbonate materials. Polycarbonate is a versatile plastic that is used to make a wide variety of consumer, industrial, and medical products. Polycarbonate offers outstanding impact resistance with good stiffness and strength. Zelux is a transparent material. Zelux GS is a gamma sterilizable medical grade that is used for making impact-resistance components found in a variety of medical and surgical device applications.
Impact Resistance
Dielectric Properties
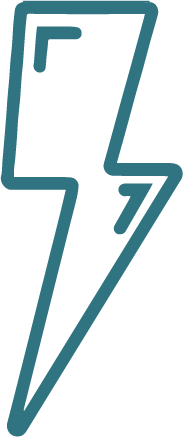
Whether you are designing to electrically insulate components from one another or protect sensitive devices from the damaging effects of electrostatic discharge, Westlake Plastics provides engineers with polymers as solutions for their most challenging electrical applications.
Thermoplastics polymers are inherently insulative. Their high dielectric strength combined with the relative ease with which they can be manufactured into complex shapes makes them well suited to be used to insulate and isolate sensitive electronics and electrical equipment.
The Westlake Plastics’ portfolio includes Tempalux (polyetherimide), Norylux (modified polyphenyl ether) and Thermalux (polysulfone). These products offer high dielectric strength, high volume resistivity, and high heat resistance that are well suited as insulators. Additionally on the other end of the dielectric spectrum, we offer a number of products such as Zelux CN-P (polycarbonate), Pomalux CN-F (polyoxymethylene copolymer), and Absylux SD-A (Acrylonitirle Butadiene Styrene) that are designed to minimize the build-up and the discharge of electrostatic charge, which can damage microelectronics and semiconductors and can result in fire or explosions in hazardous work areas. These products offer different levels of surface and volume resistivity (electrical conductivity).
Dielectric Properties
Chemical Resistance
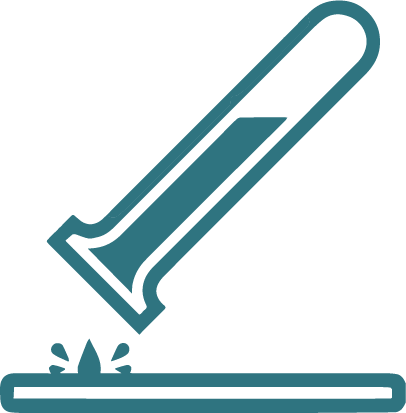
Chemical resistance refers to a material’s ability to be exposed to a chemical solution without degrading the capabilities needed for its intended use in a particular application.
When designing components, engineers must fully understand the operating environment to select the best possible chemical-resistant plastic. Exposure time, chemical concentration, heat, UV radiation, and applied or internal stresses can compound the effects that a chemical has on a thermoplastic substrate. Chemical exposure can affect the strength, stiffness, surface finish, color, dimensions, or weight of a thermoplastic substrate.
The basic modes of interaction which cause these changes are:
· Chemical attack of the polymer chain, which degrades the properties. Mechanisms of attack include oxidation, reaction of functional groups in or on the polymer chain, and depolymerization.
· Physical change, including absorption of the chemical which can result in softening and swelling of the substrate.
· Permeation of the chemical through the substrate.
· Dissolution in the chemical (solvation).
· Stress cracking from the interaction of a chemical agent and internal or external stresses.
Westlake Plastics offers a wide array of materials, from semi-crystalline thermoplastics such as Propylux (polypropylene) and Ultra Ethylux (high-density polyethylene) to fluoropolymers such as Kynar (polyvinylidene fluoride), which are used in many industrial process applications due to their high chemical resistance.
Chemical Resistance
Dimensional Stability

Dimensional stability is the ability of a material to maintain its dimensions when subjected to varying degrees of heat, moisture, pressure, or other stressors. Attributes that provide an indication of a material’s inherent dimensional stability include coefficient of thermal expansion, moisture absorption, and permeability.
Materials with high heat resistance, low coefficient of thermal expansion, low moisture absorption, and high permeability resistance will exhibit better dimensional stability. These characteristics of a thermoplastic are dictated by the monomer structure, the morphology of the bulk polymer, and the types of fillers and additives that might be incorporated into the material. It’s important to recognize that in addition to these inherent characteristics, the manufacturing processes used to process the material can also affect the dimensional stability of the material in its shaped form as a result of induced stresses.
These induced stresses can result from orientation effects, differential cooling, or localized heat buildup that occur when the material is being melt processed and/or through subsequent fabrication processes. These induced or residual stresses can be released during subsequent manufacturing steps or once the finished component is put into service and exposed to typical operating conditions.
Westlake’s extensive experience in melt-processing and thermally stress-relieving thermoplastics shapes allows us to deliver products with extremely low levels of residual stress. For example, our compression molded Norylux (modified polyphenylene ether) product is a high-strength amorphous thermoplastic with good heat resistance, low moisture absorption, and a low coefficient of thermal expansion. This inherently dimensionally-stable polymer, when compression molded and thermally stress relieved, results in slabs and sheets with a high degree of dimensional stability.
Dimensional Stability
Food Contact
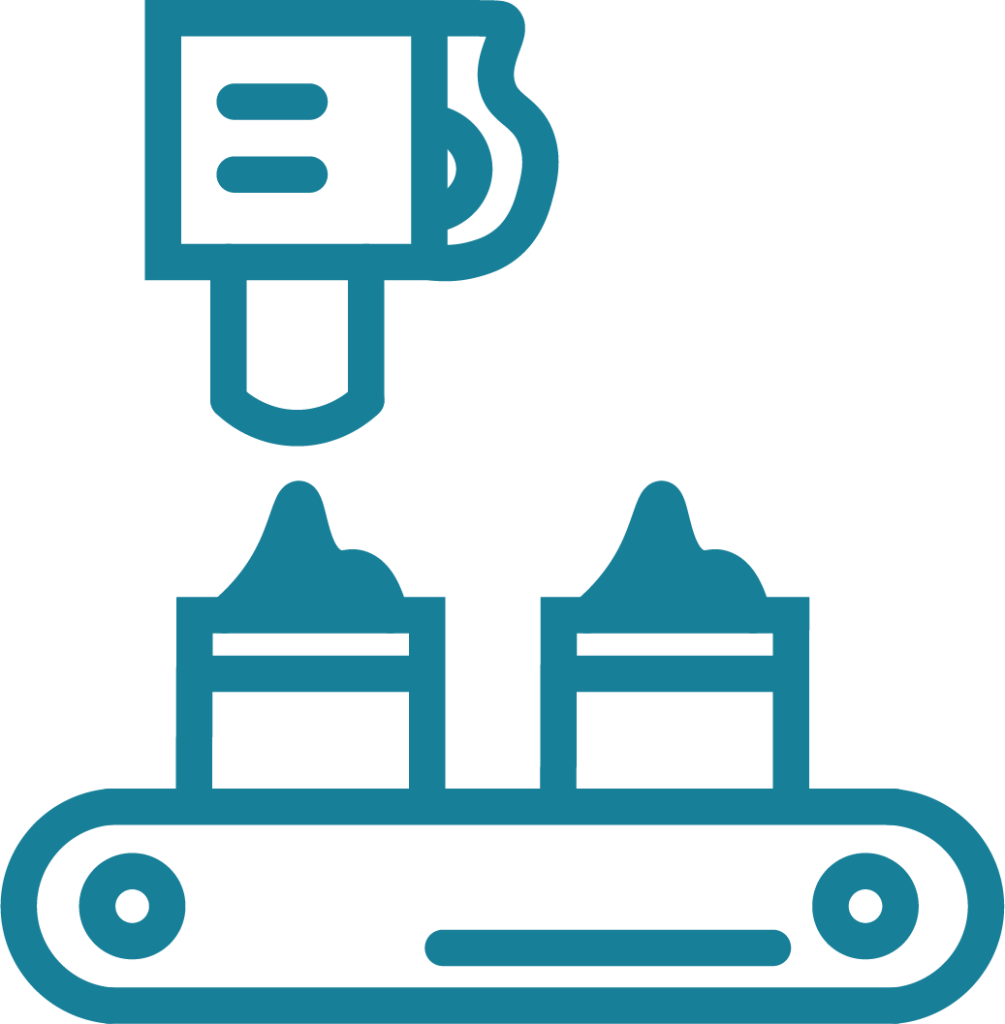
According to the FDA, a food-contact substance is “any substance that is intended for use as a component of materials used in manufacturing, packing, packaging, transporting, or holding food.”
Thermoplastics are commonly used in food-contact applications because they are lightweight, strong, heat- and chemical-resistant, flexible, tough, and durable. To be considered suitable for food contact applications, thermoplastics must comply with the standards of various regulatory agencies, such as the USDA, the FDA, and 3A Sanitary Standards. They must resistant to chemical attack and degradation from food ingredients and be resistant to leaching chemicals into the food products they come in contact with. Additionally, when used in food processing equipment thermoplastics must also be able to withstand the operating environment including exposure to dry heat, steam, cleaning solutions, and sanitization cycles.
Examples of Westlake products that are used in food processing equipment include Ultra-Ethylux (high-density polyethylene), Ethylux (low-density polyethylene), Propylux (polypropylene), Pomalux (polyoxymethylene), and Lennite (ultra-high molecular-weight polyethylene). These products are made with resins that are suitable for use in certain food contact applications. If you’re considering one of our products for use in a food contact application where compliance to a specific standard is required (e.g. FDA, USDA, and 3A Sanitary Standard ) please contact Westlake Plastics for specific regulatory declarations.
Food Contact
Wear Resistance
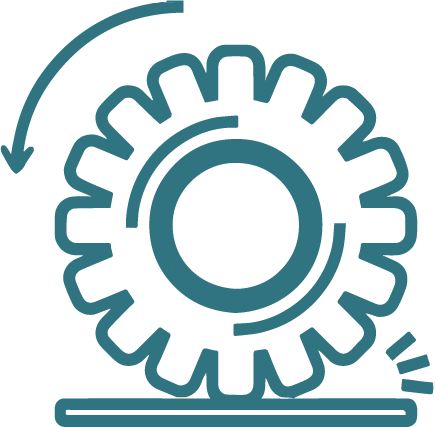
Wear of a substrate is defined as the volumetric loss of material. The rate of wear measures this volumetric loss per unit of time. A material substrates ability to resist this volumetric loss, is a measure wear resistance.
There are two types of wear mechanisms, adhesive wear and abrasive wear. Adhesive wear between two surfaces is characterized by fine particles of material being removed from the surface. The resulting debris forms a fine powder and transfers to the counter-face surface. Abrasive wear, occurs when one (typically harder) surface scrapes or abrades the counter-face. This type of wear is characterized by large gouges or grooves. It is an indication of high wear rates and/or that the pressure velocity (PV) limits of the material have been exceeded.
Wear rates for adhesive wear can be estimated by the equation W = KPV*T, where W = volumetric wear P = pressure, V = velocity, T = elapsed time, and K = the material related variable and is defined as the material wear factor. The lower the K, the more wear-resistant the plastic. K should only be used as a relative performance measure when comparing thermoplastic alternatives.
Wear can be quantified through tests including Taber Abrasion Test (ASTM D1044) and Method for Measuring Wear Rate and Coefficient of Friction of Materials (ASTM D3702). Controlling wear and friction can deliver numerous benefits, including reduced maintenance, higher efficiency, and higher load bearing and run speeds. Compared to metals, thermoplastics offer improved wear and corrosion resistance and reduced weight and lower inertia.
Semi-crystalline materials typically exhibit good wear resistance. Commonly used plastics include Pomalux (polyoxymethylene copolymer), PA6/6, Arolux PEEK (polyetheretherketone), and Lennite (ultra-high molecular-weight polyethylene).
Wear Resistance
Heat Resistance
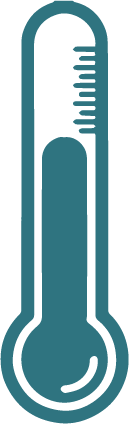
For applications where materials will be exposed to elevated temperatures, one must know how heat resistant the material is. Heat resistance of a thermoplastic material can be quantified in several ways. As an example, short term heat resistance can be quantified by considering the materials heat deflection temperature (HDT) following ASTM D648 or ISO 75. Unfortunately, this test only illustrates short term performance, measuring the effect of temperature on stiffness.
Another test, Continuous Use Temperature (CUT), is a heat aging test defining the maximum temperature at which a material retains 50% of its initial performance following 100,000 hours of continuous exposure. Underwriters Laboratory (UL) 746B Standard for Polymeric Materials – Long Term Property Evaluations, also referred to as Relative Temperature Index (RTI) testing, is a standardized test for determining CUT. Because properties of a material vary in their response to heat aging, RTI values are reported for 3 categories: Electrical properties, Tensile properties, and Impact properties.
Although this test provides insight into how the material “ages” in the presence of heat, continuous use temperature does not define a materials ability to handle a load at a specific temperature. To determine this, a materials creep resistance and fatigue strength must also be considered. For applications where materials will be exposed to elevated temperatures is a complex problem, and it is important to consider the long-term effects of heat exposure on the materials properties. While Relative Temperature Index has its limitations, it is an established method for understanding the long-term effects of heat exposure.
Westlake Plastics offers a number of materials with high heat resistance including, Arolux PEKK (polyetheretherketone), Arolux PPS (polyphenyl sulfide), Thermalux PPSU (polyphenylsulfone), Thermalux PES (polyethersulfone), Tempalux (polyethylenimine), and Kynar and Fluorolux (polyvinylidene difluoride). All these materials in unfilled/unreinforced form have RTI ratings of ≥ 150°C (302°F).
Heat Resistant
Transparent/Optical Properties

A number of factors impact the optical properties of polymers, including morphology, types of additives, stabilizers, and colorants. Manufacturing processes can impart residual stresses which can also affect optical properties.
Optical properties of polymers include:
· Haze, which provides an indication of how light is scattered within a transparent polymer.
· Yellowness index, which is a number calculated from spectrophotometric data that describes the change in color of a test sample from clear or white to yellow. This test is commonly used to define color changes in a material caused by real or simulated outdoor exposure.
· Refractive index, which is an indicator of the impact of additives or heat treatments when light is transmitted through transparent materials.
· Specular gloss, which is the ability of a polymer surface to reflect light in a certain direction.
· Light Transmittance, which is when light moves through a transparent material where it can be transmitted, absorbed, or reflected. Transmittance is the proportion of incident light that moves all the way through to the other side.
Traditional, commonly used transparent plastics include, Zelux (polycarbonate), PET (polyethylene terephthalate), acrylic, butyrate, and general-purpose Styron (polystryrene). Next generation transparent polymers include Amidelux (clear nylon) and Cylux (cyclic olefinic copolymer). Our Amidelux and Cylux COC materials provide outstanding optical properties, combined with excellent impact and chemical resistance, offering designers and engineers greater design freedom.
Transparent